Keeping the System Running: Best Practices for Automated System Maintenance
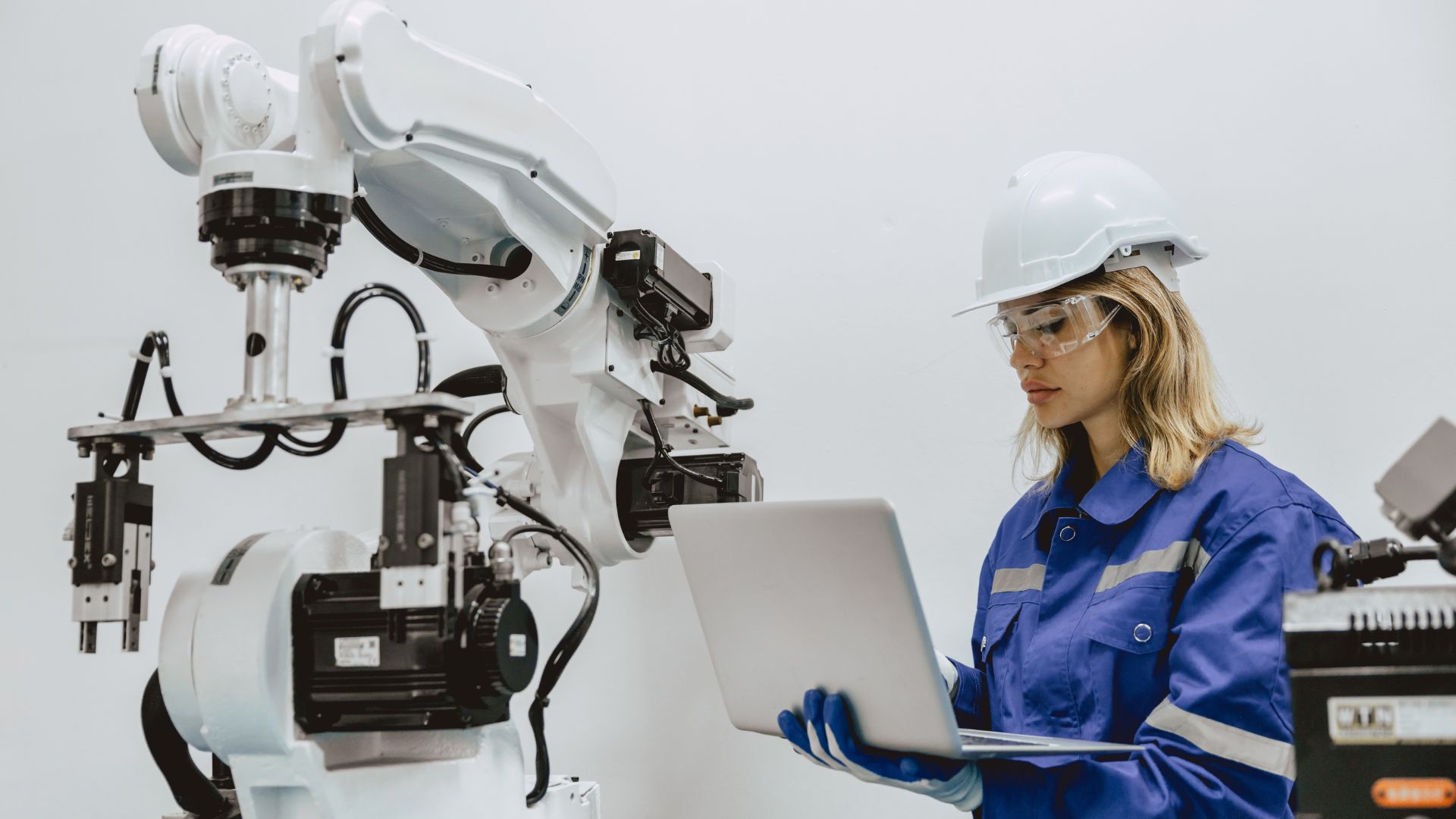
Automated systems are powerful tools for efficiency, but like any technology, they require proper maintenance to ensure long-term performance. Implementing best practices for maintenance can prevent costly breakdowns and keep automation systems running smoothly.
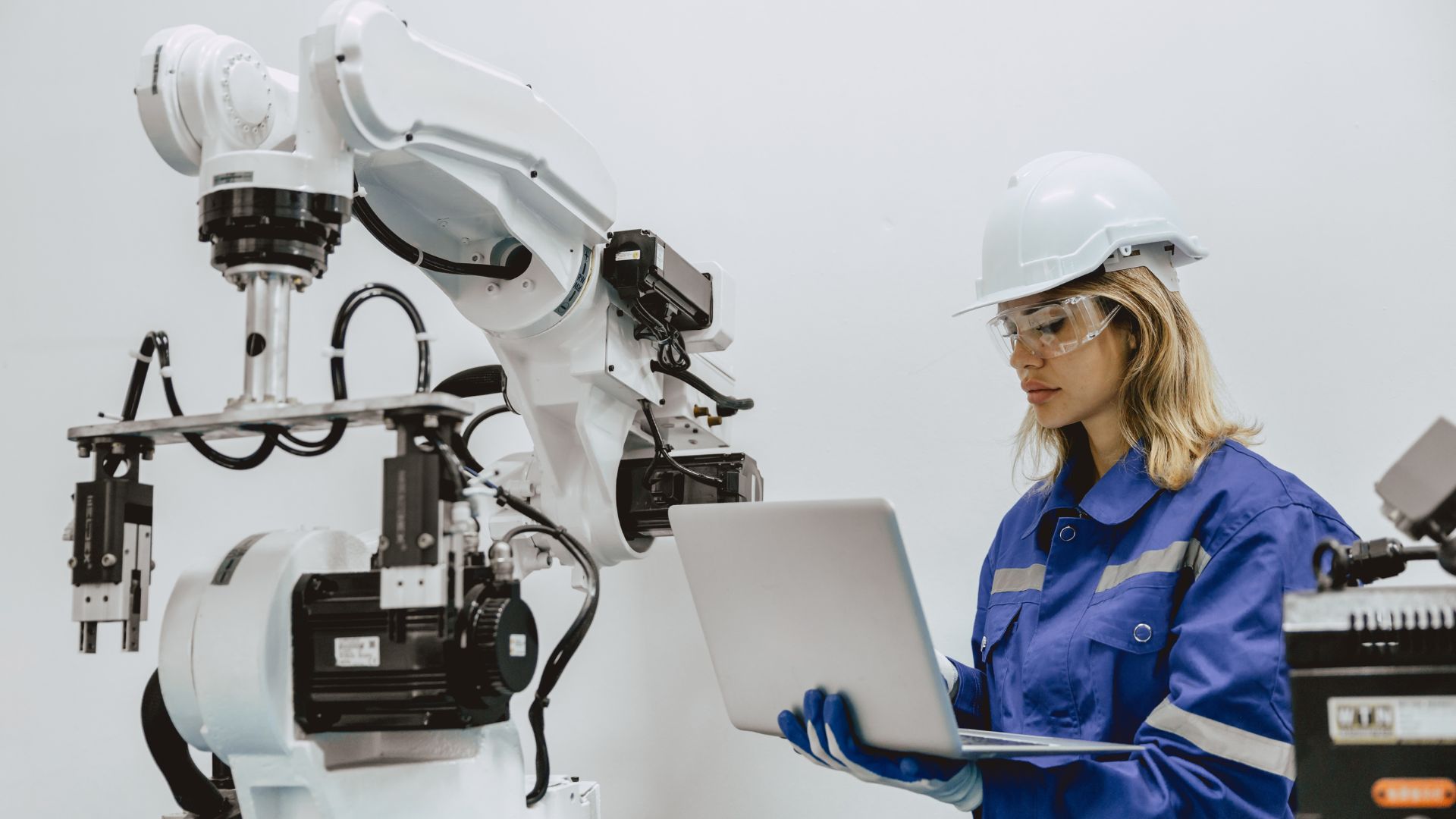
One of the most effective maintenance strategies is predictive maintenance. Using sensors and data analytics, automated systems can detect early signs of wear and tear, allowing for repairs before a failure occurs. This approach minimizes downtime and reduces the risk of unexpected disruptions.
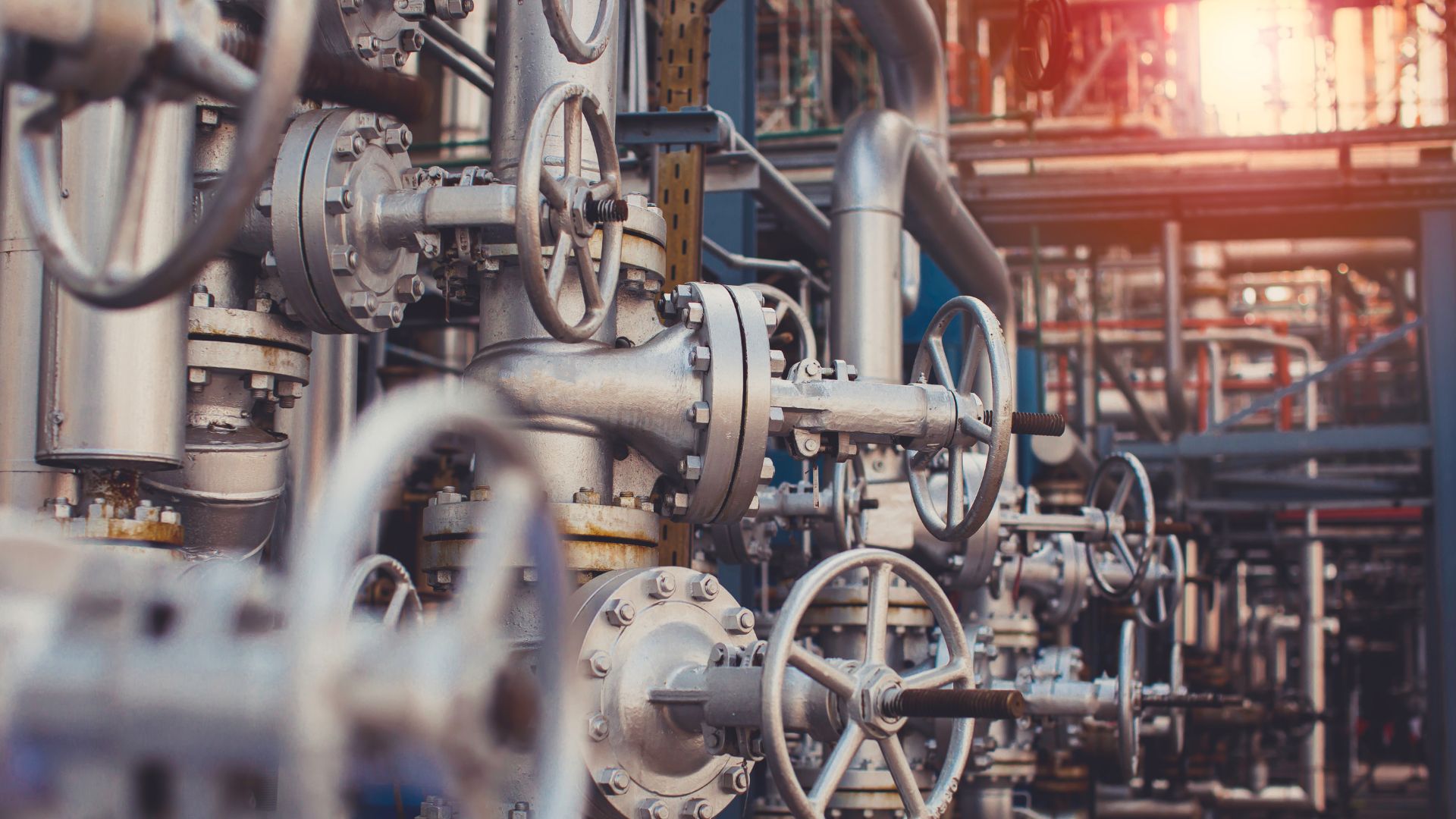
Routine inspections are also crucial. Regularly checking robotic arms, conveyor belts, and control systems ensures that minor issues are addressed before they escalate. Many companies use automated diagnostic software to monitor system health and alert operators to potential problems.
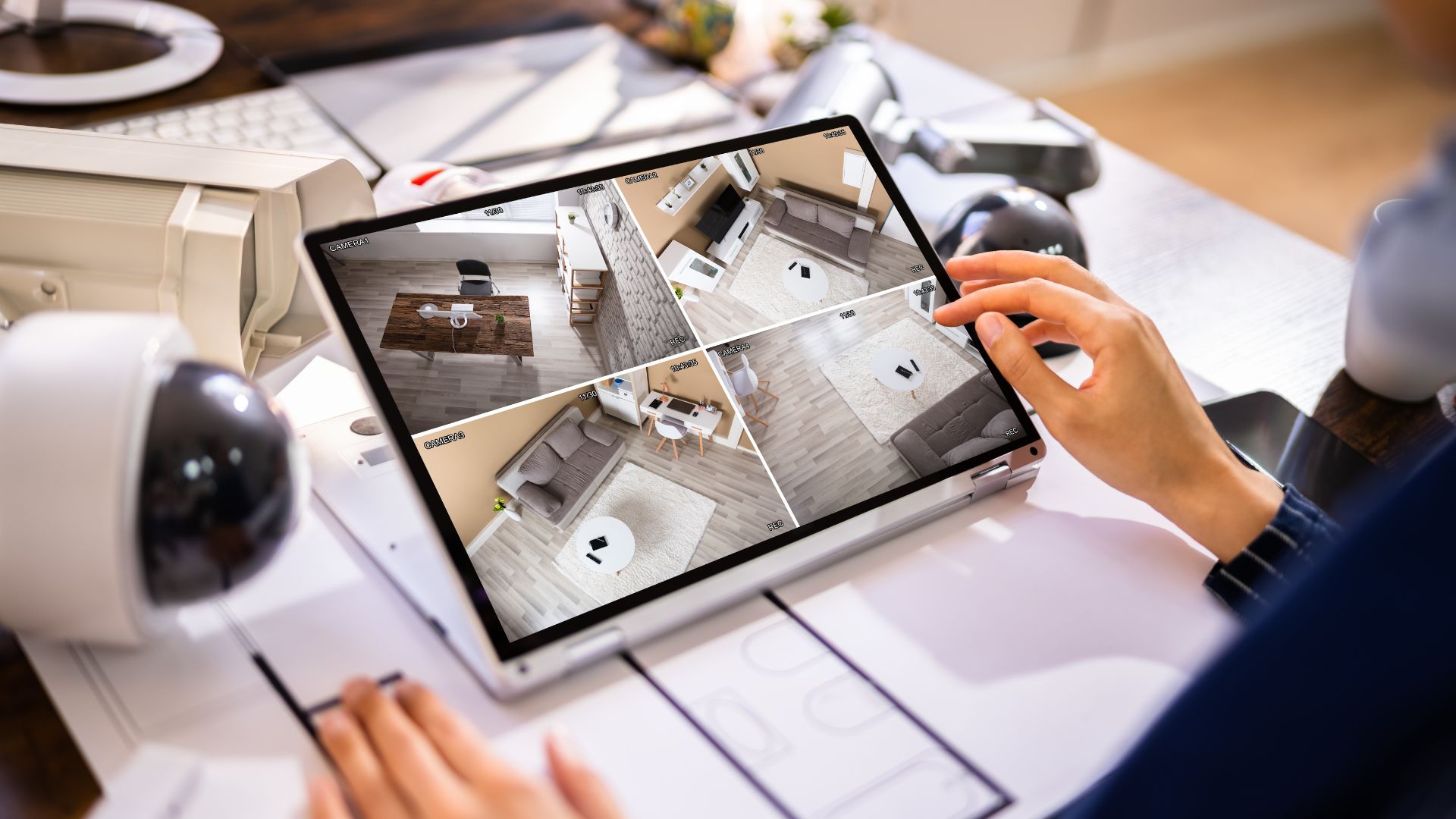
Keeping software and firmware up to date is another key factor. Manufacturers frequently release updates to improve system performance and security, so ensuring that automation software is current helps maintain efficiency and reliability.
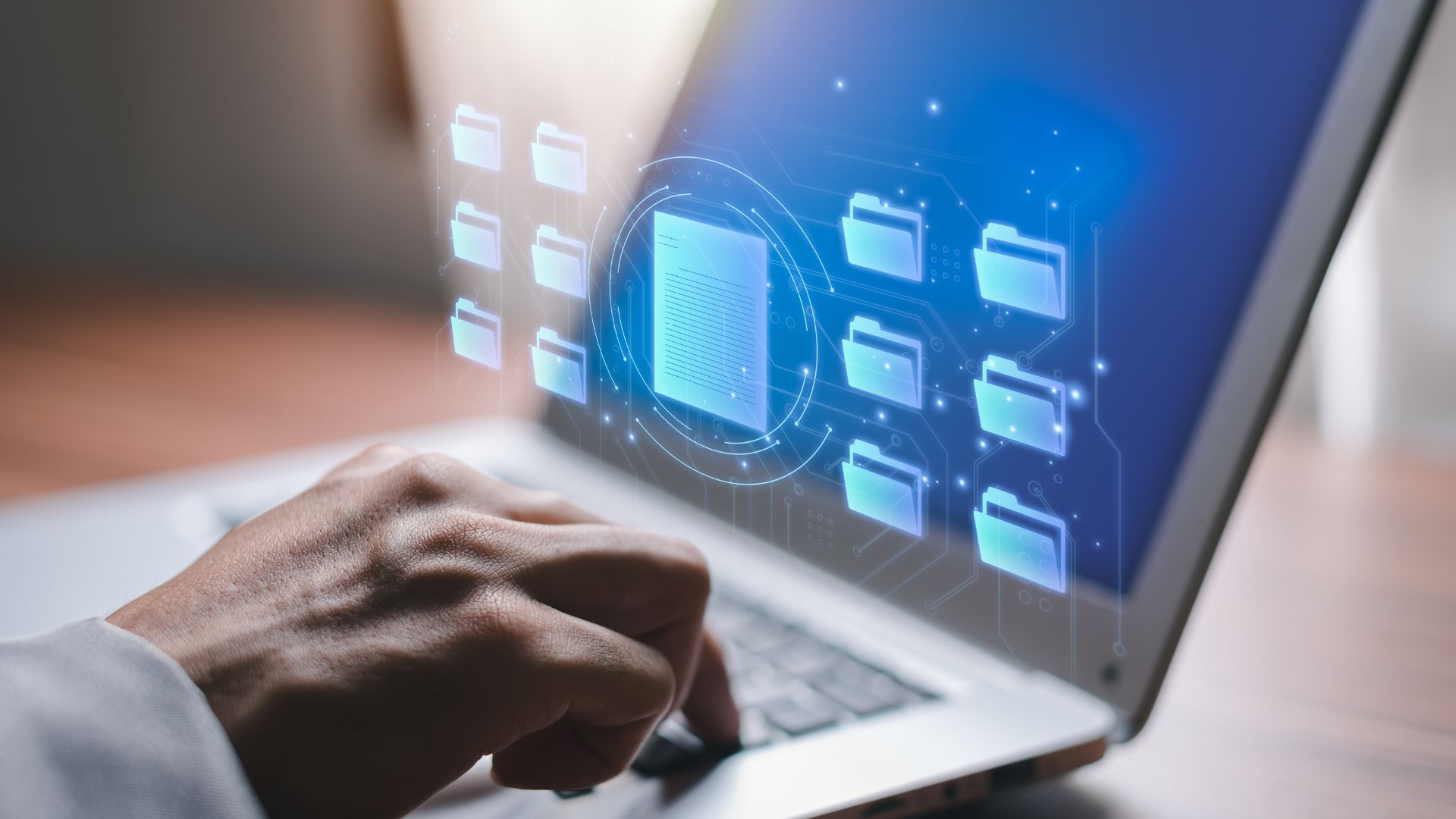
By implementing these best practices, businesses can maximize the lifespan and effectiveness of their automated systems, ensuring smooth operations and continued success.